切削液润滑剂的合成方法
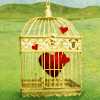
切削液润滑剂的合成方法通常包括以下几个步骤:
1. 基础油的选择:
切削液的基础油通常由矿物油、合成油或植物油构成。矿物油成本较低,但可能存在环保和生物降解性较差的问题;合成油具有更好的热稳定性和化学稳定性,适用于高温和重负荷加工;植物油环保且生物降解性好,但可能影响切削液的使用寿命。
2. 添加剂的配制:
添加剂是切削液性能的关键,包括极压剂、防锈剂、防腐败剂、消泡剂、表面活性剂等。极压剂如硫化物、氯化物、磷酸盐等,能提供润滑保护,防止刀具和工件表面的磨损;防锈剂如亚硝酸钠、苯骈三氮唑等,防止金属表面氧化;防腐败剂如有机酸、季铵盐等,抑制细菌和霉菌生长;消泡剂如硅油、改性聚醚等,消除加工过程中产生的泡沫;表面活性剂如磺酸盐、醇醚等,提高切削液的润湿性和渗透性。
3. 配方设计:
根据切削液的使用环境、加工材料、工艺条件等因素,设计合适的配方。这需要考虑切削液的冷却、润滑、清洗和防锈性能,以及对操作者安全和环境影响的平衡。
4. 混合与制备:
将基础油和添加剂按照设计比例在搅拌设备中混合,确保所有成分均匀分散。在混合过程中,可能需要控制温度和搅拌速度,以优化添加剂的溶解和分散效果。
5. 测试与调整:
制备完成后,对切削液进行一系列性能测试,如润滑性、冷却性、防锈性、生物稳定性等。根据测试结果,可能需要调整配方,以达到最佳的使用效果。
6. 包装与储存:
将合格的切削液装入合适的容器中,确保包装密封良好,防止空气、水分和微生物的进入。储存时应避免阳光直射,保持在适宜的温度和湿度条件下。
1、切削液的分类
切削液按照其基础油和添加剂的不同,主要可以分为以下几类:
1. 水基切削液:以水为主要成分,添加极压剂、防锈剂、表面活性剂等,具有良好的冷却效果,但润滑性能相对较弱,适用于轻负荷和高速切削。
2. 油基切削液:以矿物油或合成油为基体,极压性能优异,适用于重负荷切削,但冷却效果较差,且可能产生烟雾和火灾风险。
3. 乳化液:水基切削液中加入乳化剂,形成稳定的油水乳液,兼具水基和油基切削液的优点,适用于中等负荷切削。
4. 合成切削液:以合成油为基体,添加各种添加剂,具有良好的热稳定性和化学稳定性,适用于高温和特殊材料的切削。
5. 半合成切削液:介于水基和合成切削液之间,部分以合成油替代矿物油,提供更好的润滑性能,同时保持一定的冷却效果。
2、切削液的使用注意事项
使用切削液时,需要注意以下几点:
1. 定期检测和更换:切削液在使用过程中会逐渐消耗添加剂,产生微生物,因此需定期检测其性能,及时补充添加剂或更换新的切削液。
2. 过滤系统:设置过滤系统,去除切削液中的金属屑、油泥等杂质,保持切削液的清洁。
3. 维护环境卫生:切削液使用过程中产生的雾气和废液应妥善处理,避免对操作环境和工人健康造成影响。
4. 合理配比:根据切削条件和工件材料,选择合适的切削液类型和配比,以达到最佳的加工效果。
5. 个人防护:操作人员应穿戴适当的防护装备,如防护眼镜、手套等,避免切削液直接接触皮肤和眼睛。
通过科学的合成方法和合理的使用管理,切削液能够显著提高切削效率和加工质量,同时保障操作人员的健康和环境的可持续性。