磨削液的分类和选用选择
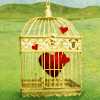
磨削液的分类主要包括水基磨削液、油基磨削液和合成磨削液三大类。选用磨削液时,需要考虑加工材料、工件精度、工件表面质量、冷却效果、润滑性能以及环保和成本等因素。
1. 水基磨削液:
乳化液:由矿物油和表面活性剂组成,通过乳化形成稳定的油水混合物,具有良好的冷却效果,适用于钢和铸铁的磨削。
化学合成液:由水、防锈剂、极压添加剂等组成,对环境友好,冷却和润滑性能较好,适用于各种金属材料的磨削。
2. 油基磨削液:
矿物油:纯油性磨削液,润滑性能极佳,但冷却效果较差,适用于加工精度要求不高、对工件表面质量要求高的场合。
极压油:添加了极压添加剂的油基磨削液,适用于重负荷磨削,如铝合金、铜合金等软金属的加工。
3. 合成磨削液:
合成切削液:由水和多种有机化合物组成,具有良好的冷却、润滑和防锈性能,对环境影响小,适用于精密磨削和高速磨削。
微乳化液:介于水基和油基之间,既有良好的冷却效果,又有一定的润滑性能,适用于加工硬质合金和高温合金。
1、磨削液的更换周期
磨削液的更换周期受多种因素影响,如工件材料、磨削条件、使用频率、维护状况等。一般来说,水基磨削液的更换周期较短,可能需要每2-4周更换一次,或者根据磨削液的浊度、pH值和细菌含量进行定期检测,一旦超标就需要更换。油基磨削液的更换周期相对较长,可能每3-6个月更换一次,但也要根据实际使用情况和检测结果来确定。在更换磨削液时,应彻底清洗冷却系统,避免旧液残留影响新液的性能。
2、磨削液的维护
磨削液的维护主要包括以下几点:
定期检测:定期检查磨削液的pH值、浊度、细菌含量等指标,确保其性能稳定。
补充添加剂:根据磨削液的消耗情况,适时补充防锈剂、极压剂等添加剂,保持其功能。
过滤:使用过滤设备定期清除磨削液中的金属屑、砂粒等杂质,防止堵塞喷嘴和冷却系统。
清洁:保持磨削液循环系统的清洁,定期清洗油箱、管道和喷嘴,防止细菌滋生和油泥积累。
更换:根据磨削液的使用情况和制造商的建议,适时更换磨削液,避免因长时间使用导致性能下降。
选择和维护磨削液是保证磨削加工质量、延长刀具寿命、提高生产效率和降低生产成本的重要环节。根据实际加工条件和要求,合理选择磨削液类型,并进行有效的维护,能有效提升磨削加工的综合性能。