数控车床对刀与程序之间如何建立联系
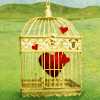
数控车床对刀与程序之间通过以下步骤建立联系:
1. 对刀操作:
对刀是确定刀具相对于工件坐标系位置的过程。在数控车床上,通常通过以下步骤进行对刀:
手动对刀:操作员手动移动刀具,使其与工件接触,然后记录下刀具与工件的相对位置。
自动对刀:使用对刀仪或自动对刀装置,通过传感器测量刀具与工件的相对位置,系统自动记录数据。
刀具长度补偿:在对刀后,系统会记录刀具的实际长度,以便在编程时进行补偿,确保刀具的实际切削长度与程序设定的一致。
2. 编写程序:
在对刀完成后,需要根据对刀结果编写或修改数控程序。程序中包含刀具的运动轨迹、切削参数(如进给速度、主轴转速等)以及刀具的更换指令。以下是程序中与对刀相关的部分:
G代码和M代码:G代码用于指定刀具的运动,如G00快速移动,G01线性插补等。M代码用于控制机床的辅助功能,如M03主轴正转,M05主轴停止等。
刀具偏置:在程序中,可以通过T代码指定刀具号,同时通过G43(刀具长度补偿加)或G44(刀具长度补偿减)指令来应用对刀结果。
工件坐标系设定:根据对刀结果,可能需要设定或调整工件坐标系(WCS),确保刀具在正确的起点开始切削。
3. 程序验证:
编写好程序后,需要进行模拟或试切验证。在模拟阶段,通过软件模拟刀具的运动轨迹,检查是否有干涉、碰撞等问题。在试切阶段,实际运行程序,观察刀具的切削效果,根据需要调整程序参数。
4. 生产运行:
确认程序无误后,即可在实际生产中运行程序。系统会根据程序指令控制刀具的运动,按照预设的路径和参数进行切削,从而实现精确的零件加工。
1、数控车床对刀方法
数控车床对刀方法主要有以下几种:
试切对刀:通过切削工件,测量切削后的尺寸,然后调整刀具位置,直到得到正确的尺寸。
对刀仪对刀:使用对刀仪测量刀具与工件的相对位置,对刀仪通常有机械式和光学式两种,可以精确测量刀具长度和角度。
自动对刀系统:高级的数控系统配备自动对刀系统,如接触式传感器或激光对刀系统,可以自动测量刀具与工件的相对位置,简化对刀过程。
程序对刀:通过编写专门的对刀程序,让刀具在特定的对刀点进行运动,通过测量或传感器反馈来确定刀具位置。
2、数控车床对刀注意事项
在数控车床对刀过程中,需要注意以下几点:
安全第一:操作时要佩戴防护眼镜和手套,确保手指远离旋转的刀具和工件。
精度要求:对刀精度直接影响零件加工质量,因此对刀时要保证精度,避免误差累积。
刀具选择:使用合适的刀具,确保刀具的刚性和耐用性,避免在对刀过程中损坏刀具。
程序验证:对刀后务必验证程序,确保刀具运动路径正确,避免在实际生产中出现意外。
定期校准:定期对机床进行校准,以确保机床的精度,减少对刀误差。
通过精确的对刀操作和程序编写,数控车床能够实现高精度的零件加工,提高生产效率和产品质量。