模具刀口怎么磨才好
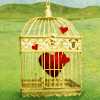
模具刀口的磨削方法需要根据刀口材料、形状和精度要求来选择合适的工具和步骤。以下是一种常见的磨削方法:
1. 工具准备:首先,准备好所需的工具,包括砂轮机、金刚石砂轮、细砂纸、千分尺、直尺、测量显微镜等。
2. 预处理:确保模具刀口表面清洁,无油污和杂质,以免影响磨削效果。如果刀口有锈蚀,可以先用砂纸进行粗磨。
3. 粗磨:使用粗粒度的金刚石砂轮,对刀口进行初步的形状修复和尺寸调整。注意保持砂轮与刀口的接触角度,以防止过度磨损或产生不均匀的磨痕。
4. 精磨:使用中粒度的金刚石砂轮,对刀口进行精细磨削,以达到所需的尺寸精度和表面粗糙度。此时,要控制好砂轮的转速和进给速度,确保磨削均匀。
5. 抛光:使用细砂纸或抛光轮进行抛光,以提高刀口的光洁度。可以使用油石或抛光膏来辅助抛光,以减少划痕和提高光亮度。
6. 检查:使用千分尺、直尺和测量显微镜等工具,对磨削后的刀口进行尺寸和形状的精确测量,确保符合设计要求。
7. 冷却:在磨削过程中,要定期给刀口和砂轮浇水冷却,防止过热导致刀口变形或硬度降低。
8. 保养:磨削结束后,清理工具和工作台,对刀口进行防锈处理,以延长使用寿命。
1、模具刀口的材料选择
模具刀口的材料选择对刀口的性能和寿命至关重要。常见的刀口材料有高速钢、硬质合金、陶瓷和金刚石等。
1. 高速钢:具有良好的韧性和可加工性,适用于制造中低速、中低精度的模具刀口。
2. 硬质合金:硬度高、耐磨性好,适用于高速、高精度的模具刀口,但价格相对较高。
3. 陶瓷:耐高温、耐磨损,适用于高温环境和高精度要求的模具刀口,但抗冲击性较差。
4. 金刚石:硬度最高,耐磨性极好,适用于高精度、高硬度的模具刀口,但成本极高且易碎。
选择材料时,需要考虑刀口的使用环境、加工速度、精度要求以及成本预算等因素。
2、模具刀口的磨损原因
模具刀口的磨损主要由以下几个原因造成:
1. 机械磨损:在切削过程中,刀口与工件之间产生摩擦,导致刀口表面材料的逐渐脱落。
2. 热磨损:高速切削时,刀口与工件接触区域产生大量热量,可能导致刀口材料软化或熔化,形成磨损。
3. 化学磨损:刀口与工件材料发生化学反应,导致刀口表面的化学侵蚀。
4. 疲劳磨损:反复切削导致刀口材料内部产生微裂纹,最终导致刀口整体强度下降。
5. 冲击磨损:在切削硬质材料或不规则形状工件时,刀口可能受到冲击,导致局部磨损或崩刃。
了解磨损原因有助于选择合适的刀口材料和磨削方法,以及采取适当的预防措施,如使用冷却液、优化切削参数等,以延长刀口的使用寿命。
通过选择合适的磨削方法、材料和保养措施,可以有效提高模具刀口的性能和使用寿命,确保模具的正常工作。